
About
There is a growing interest in infrared (IR) imaging systems for a wide range of applications from military night vision systems to automotive and consumer electronics. Detection mechanism of infrared can be classified into two groups: photon detection and thermal detection. In the evolution of modern infrared detection systems, photon detectors have played a major role due to their fast response time and high detectivity. However, photon detectors are expensive for general commercial applications because cryogenic cooling is required to suppress the thermal noise from the detecting material which is typically low-bandgap semiconductor. Recently, thermal detectors have been widely used for uncooled thermal imaging systems due to their low cost. Enabled by using micromachining technology, good thermal isolation structures can be easily formed for uncooled IR Focal Plane Arrays (FPAs), providing a sensitivity high enough for portable military applications as well as low cost commercial applications.
Bolometers are thermistor-based detectors that measure temperature change in a thermally-isolated membrane heated by infrared radiation absorbed on the surface. Micromachined membrane structure should provide not only good thermal isolation from the substrate but also a high fill-factor and good IC process compatibility. It is generally true to achieve a higher fill-factor in array structures by using surface micromachining than bulk micromachining technology. Typically, IR absorbing areas are formed by a micromachined membrane suspended by two or four arms in the same plane over etched pits on the substrate. The longer the length of the suspended arms becomes in order to achieve good thermal isolation, the smaller the membrane size in the fixed pixel pitch, resulting in a lower fill-factor. None of previous works has achieved a fill-factor higher than 60% in the pixel pitch smaller than 50um. We proposed a high fill-factor bolometer using multi-level electrothermal structures.
Figure 1 shows the thermal isolation structure of the proposed bolometer. Good thermal isolation can be achieved from optimizing the arm dimension and layout between anchor and post. On the top of the thermal isolation arms the IR absorbing membrane covers almost the entire pixel to achieve a high fill-factor over 92%. Thermal isolation can be independently optimized without sacrificing IR absorbing area to achieve high fill-factor. Titanium was used as temperature sensing material because it has a relatively high TCR (Temperature Coefficient of Resistance), low noise characteristics, and is compatible with IC processes.
Bolometers are thermistor-based detectors that measure temperature change in a thermally-isolated membrane heated by infrared radiation absorbed on the surface. Micromachined membrane structure should provide not only good thermal isolation from the substrate but also a high fill-factor and good IC process compatibility. It is generally true to achieve a higher fill-factor in array structures by using surface micromachining than bulk micromachining technology. Typically, IR absorbing areas are formed by a micromachined membrane suspended by two or four arms in the same plane over etched pits on the substrate. The longer the length of the suspended arms becomes in order to achieve good thermal isolation, the smaller the membrane size in the fixed pixel pitch, resulting in a lower fill-factor. None of previous works has achieved a fill-factor higher than 60% in the pixel pitch smaller than 50um. We proposed a high fill-factor bolometer using multi-level electrothermal structures.
Figure 1 shows the thermal isolation structure of the proposed bolometer. Good thermal isolation can be achieved from optimizing the arm dimension and layout between anchor and post. On the top of the thermal isolation arms the IR absorbing membrane covers almost the entire pixel to achieve a high fill-factor over 92%. Thermal isolation can be independently optimized without sacrificing IR absorbing area to achieve high fill-factor. Titanium was used as temperature sensing material because it has a relatively high TCR (Temperature Coefficient of Resistance), low noise characteristics, and is compatible with IC processes.
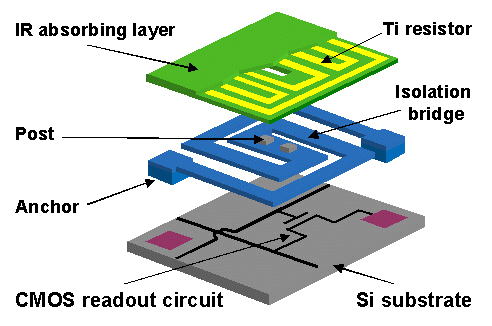
Figure 1
Figure 2 shows the fabrication process steps. First, the polysilicon sacrificial layer is defined on the substrate wafer, which includes on-chip CMOS readout circuitry and passivation layers. Titanium thin-film is patterned to make a connection between the substrate contact (anchor) and the post. Titanium metal film is sandwiched between PECVD deposited silicon oxinitride layers to prevent oxidation and release the stress. Additional contact (post) is formed to connect the metal thin-film to the serpentine resistive pattern on the absorbing membrane defined on the top of the second sacrificial layer. Finally, the sacrificial layer is removed by isotropic dry etching (XeF2) process. The silicon oxinitride membrane is optimized to give low residual stress. Figure 3 shows the fabricated test structures. It shows a high fill-factor array can be implemented in multi-level electrothermal structures. The membrane size is 50mm¡¿50mm.
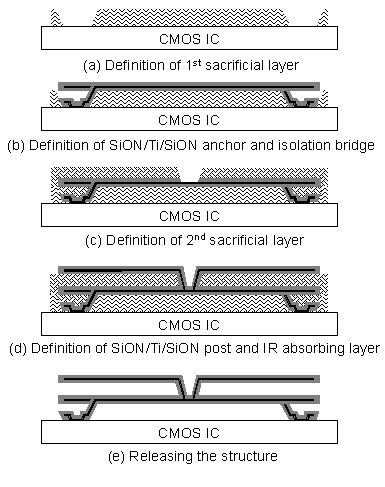
Figure 2
Figure 3 and 4 are the pictures of fabricated structure. In both pictures one can see arm structure for thermal isolation.
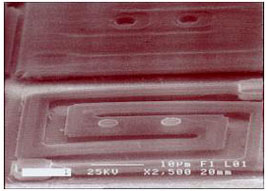
Figure 3
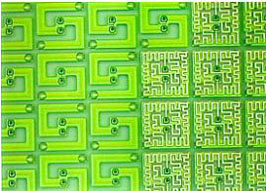
Figure 4
We measured the spectrial response and noise of proposed bolometer in vacuum, which are displayed by figure 5 and 6. Then we estimated the detectivity from measured responsivity and noise. The measuered responsivity is 1600V/W and the thermal time constant is 12msec. Figure 6 shows the 1/f noise characteristics of Ti resistor. We estimated the rms noise assuming 64KHz noise bandwidthand and then the detectivity. The detectivity was estimated about 5x10^8.
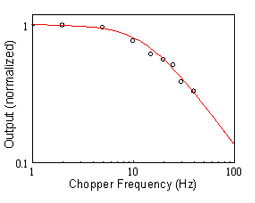
Figure 5
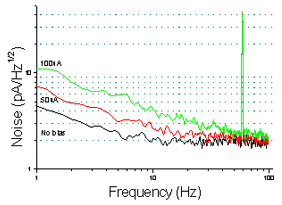
Figure 6
We proposed and verified a high-fill factor bolometer structure. The fill-factor and thermal isolation can be optimized independently, which is a good advantage for high performance bolometer.
Related Publications
- Hyung-Kew Lee, Jun-Bo Yoon, and Eusik Yoon, Sang-Baek Ju, et al. "A High fill factor Infrared Bolometer using Micromachined Multilevel Electrothermal structures," IEEE Tranactions on Electron Devices, Vol. 46, No. 7, July 1999
- Hyung-Kew Lee, Jun-Bo Yoon, Euisik Yoon, Sang-Baek Ju, Yoon-Joong Yong, Wook Lee, Sang-Gook Kim, "A High fill factor IR Bolometer using Multi-level Electrothermal structures" Electron Devices Meeting, 1998