
A Capacitive Proximity Sensor in Dual Implementation
with Tactile Imaging Capability on a Single Flexible Platform for Robot Assistant Applications
The evolution of robot engineering has made a spectacular progress for the past decade, especially in the area of humanoids as we can see in HUBO or ASIMO. Some commercial robots are available such as Roomba, although they are still in a primitive form of assistant robots. Those robots often have arm-like manipulators to handle objects. In order for those robots to interact with human being and environment safely, it is imperative to be able to detect not only tactile information but also proximity of objects or obstacles before they are too close. This function will prevent the robots from accidental collision which can bring damage to human or to robots themselves. In this work, we have proposed and demonstrated a dual mode proximity sensor which can detect not only proximity but also touch of an object for robot assistant applications. The sensor operates in two modes: proximity mode and tactile mode. Initially, the sensor operates in proximity mode until it touches an object. When the proximity mode detects the contact of any objects, the sensor will switch its mode into tactile sensing mode for acquiring an image from an object. We have used the same platform that we developed for the tactile sensor which was presented in the last MEMS conference. In the current work, we have assessed if the existing platform is suitable for dual implementation. We have tested various designs and configurations in a simple PCB fixture in order to determine the proper electrode configuration of the proximity sensor. We found that the best detection range has been obtained from the largest electrodes with the smallest gap. This implies that the dual implementation is quite plausible in the original tactile sensor platform which has a 1 mm gap between electrodes and 22 mm in length. Finally, we have demonstrated that proximity detection up to 10 cm is possible in the dual implementation in a flexible platform with adequate electrode configuration and sensing circuitry.
Figures
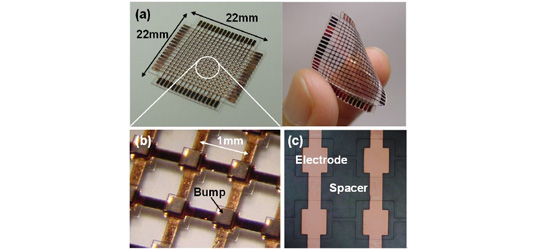
Figure 1. (a) Fabricated tactile sensor module, (b) magnified view of cells and (c) bottom electrodes and spacer layer of four tactile cells.

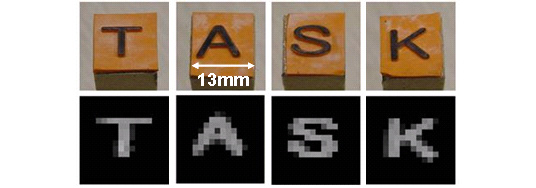
Figure 2. Flipped photographs of rubber stamps and their tactile images captured by the fabricated tactile sensor module.

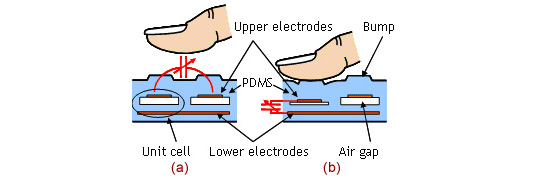
Figure 3. Conceptual diagram of the proposed dual mode proximity sensor and its operation, (a) proximity mode operation and (b) tactile mode operation.

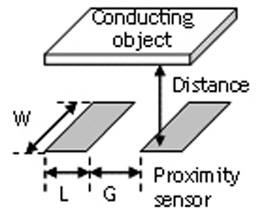
(a)
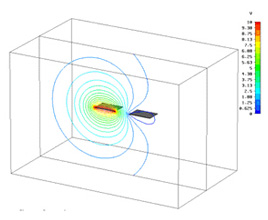
(b)
Figure 4. (a) Schematic diagram of a proximity sensor and (b) its simulation model.

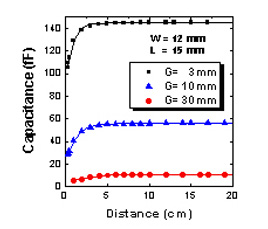
(a)
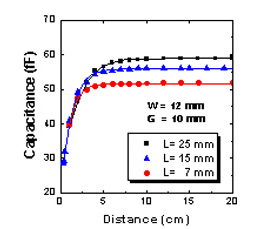
(b)
Figure 5. Measurement results of PCB proximity sensors as a function of (a) gap between electrodes and (b) length of electrodes.

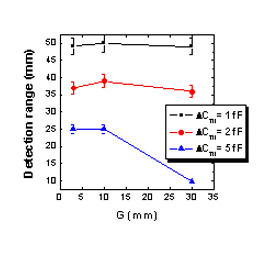
(a)
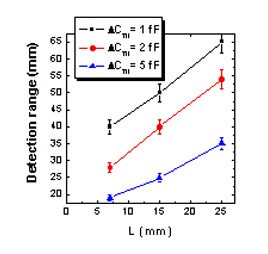
(b)
Figure 6. Measured detection range of PCB proximity sensors as a function of (a) gap between electrodes and (b) electrode length for various threshold capacitance change (DCTH)

Movies
Proximity Demonstration
Tactile Demonstration

Related Publications
- Hyung- Kew Lee, Sun-Il Chang, Kyung-Hyun Kim, Seong-Jin Kim, Kwang-Seok Yun, and Euisik Yoon, "A modular expandable tactile sensor using flexible polymer," IEEE International Conference on MEMS 2005.
- Hyung-Kew Lee, Sun-Il Chang, and Euisik Yoon, "A Capacitive Proximity Sensor in Dual Implementationwith Tactile Imaging Capability on a Single Flexible Platformfor Robot Assistant Applications," IEEE International Conference on MEMS 2006.