[Previous
Story] [Next
Story]
SELF-ASSEMBLY REQUIRED
Harvard
team uses patterned assembly to fabricate cylindrical LED display
RON DAGANI
Throw 100 or so
light-emitting diodes (LEDs) into a vial of water,
add a patterned substrate coated with a low-melting solder, heat and shake
the contents gently for a few minutes, and voilą--a
tiny LED display assembles itself as if by magic. But it's not magic--it's
patterned assembly, a process that a Harvard University research team has
now demonstrated can be used to fabricate flexible, cylindrical displays
that light up in any desired pattern [Science, 296,
323 (2002)].
The team, headed by chemistry professor George
M. Whitesides, also reports using this
strategy to assemble a curved 5-cm2 array of about 1,560 small
silicon cubes, which were used as stand-ins for microelectronic devices.
The array was generated in minutes.
"This is definitely a 'wow' paper," comments Gregory
T. A. Kovacs, an associate professor of electrical engineering at Stanford
University. It's "very
exciting," he says, because "it shows the potential for
mass-fabrication of flexible, active, electronic systems."
To make the LED displays, Whitesides and
coworkers Heiko O. Jacobs, Andrea R. Tao, Alexander Schwartz,
and David H. Gracias start with a transparent polyimide sheet on which they
have photolithographically fashioned an array of
113 280-mm-wide copper squares connected by parallel copper wires. The
squares are coated with solder, and the sheet is curled up inside a small
vial filled with water.
Then they add the LEDs--semiconductor chips
the same size as the copper squares but with a layer of gold (anode) on the
bottom and a small circular cathode on the top. When the water is heated,
the solder melts. Gentle tumbling of the vial causes the gold bottoms of
the LEDs to glom onto the liquid solder in an
effort to minimize the solder's free surface area. This drives the assembly
of LEDs on the solder-coated copper squares.
"The solder also provides the electrical connection required to operate the device and the mechanical bond required
to hold the assembly together," the researchers explain.
To correct defects in the assembly, the Harvard team performs a sequence
of agitation steps that, in minutes, ensures that the assemblies are
defect-free.
In the final fabrication operation, the researchers use dip-coating to
apply solder to the top cathode of each LED and to the polyimide-supported
parallel copper wires of a top electrode. This electrode is manually
positioned over the LED array and fused to the individual diodes by melting
the solder on the LED and wire surfaces.
By applying a potential between the top and substrate electrodes, the
researchers can light up any or all of the 113 LEDs.
The LED components used in this array are 30 times smaller than
components used in earlier solder-based self-assembly experiments,
according to Jacobs.
In principle, Stanford's Kovacs tells C&EN, the method could be
applied to fabricating systems that are more complex. "The ability to
'dock' different elements in regular arrays--such as red, green, and blue LEDs in a color display--will be key,"
he says. He foresees "a large number of commercial applications, from
toys through high-end displays."
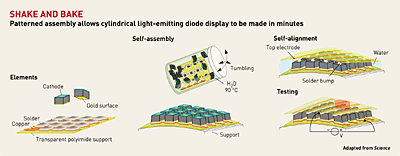
[Previous
Story] [Next
Story]
Top
Chemical & Engineering News
Copyright © 2002 American Chemical Society
|